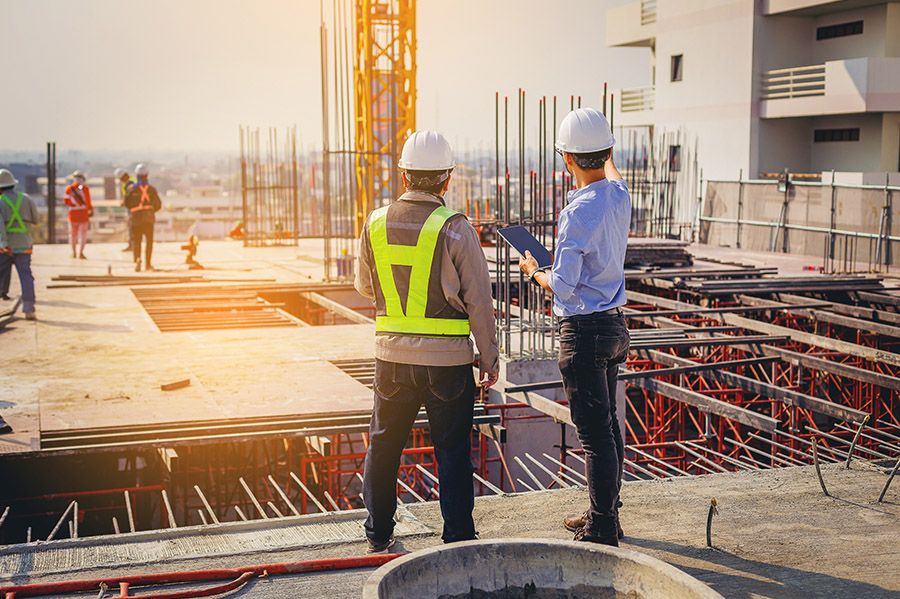
The Australian construction industry has been under pressure over the last year, and that’s likely to continue into 2023. The strain has been building up for several years, due to not having enough labourers to keep up with the demand for houses and renovations needing to be built.
Since covid introduced itself to the world, builders have had a new source of problems. On top of not enough workers, there aren’t enough construction parts for the buildings. For example, trusses (an important structure type for creating rigidity in building frames) have around a 9-month wait time before builders can get access to them. There is also roughly a 16-week waiting period for Laminated Veneer Lumber (LVL), one of the most used widely used wood products.
Stuart Allen, Chairman of Master Builders Victoria’s (MBV) country sector committee, expects that these shortages won’t be going anywhere soon, and are expected to continue into next year.
"It's widespread, but if we're just talking trusses, they're used right throughout the industry. "We are talking with designers and engineers to try and get LVL beams as an alternative to pitch a roof with, but there is a demand for those beams as well and the supply of those beams comes from overseas. Now there is a shortage of those as well as; there is demand from a lot of countries”.
These factors have been steadily building up and it means the impact is going to continue to grow. The Covid-19 lockdowns in 2020/21, and labour and parts shortages have affected the increase in supply prices. The price of timber lines has doubled in the last year, and the year-on-year cost of steel is anticipated to increase up to 50%. Another factor to consider is the gradual increase in fuel prices, and the knock-on effect this will have on shipping costs transporting materials.
These numerous conditions impose a heavy financial toll, a toll that is felt by both businesses and consumers. In September last year, 83 building and construction companies across Australia entered external administration as they tried to find ways to stay in business and support their customers. Despite the increased cost, Australians are still looking to build with the number of loans to homeowners for home renovations 77.8% percent higher than the year prior. This increased demand, paired with the other challenging circumstances, has forced many people to find patience.
"Everyone is having to wait, and it's not just the building industry. The wait on materials, and certainly the Ukraine situation has made things more uncertain because we import so many materials".
“Houses are taking 30% longer to build”
- Mr. Allen, a builder in Ballarat
Here at NPA, we want to do everything we can to minimise delays to building projects. We understand the difficulties that people and businesses are experiencing right now and are pleased to say we are taking measures to minimize supply issues.
When covid first arrived we quickly realized that things were going to get messy in no time at all and so we began preparing for any issues before they arise. We made the decision to bring in more stock than we usually would. In anticipation of shortages, we stocked our warehouse full of our most popular products, and products we thought people might need the most. We are happy to say that this was a successful move, as we continue to be able to provide our clients with the items they need, on time and when they need them!
We are particularly pleased to say we are continuing to provide support to the industry by supplying our bushings for frameworks to companies looking for solutions to support their production. For any enquiries to find out how we can support your projects, visit our website at https://www.npa.com.au/, or talk to one of our friendly staff by calling (08) 8268 2733.